Category
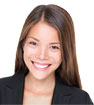
BLDC Motor Supplier

Home » BLDC Motor Wiki » Brushless DC Gear Motor Noise Troubleshooting
Brushless DC Gear Motor Noise Troubleshooting
When motor problems occur, we should check and solve them in time. The premise is that we have a certain understanding of the problems that may arise in the motor. The following ATO mainly introduces the method of noise treatment for brushless DC gear motor.
1. Damage of transmission parts
During installation, the transmission parts are damaged due to improper operation, resulting in inaccurate or unstable motion of the system. The damage of high-speed moving parts results in oil film vibration or dynamic unbalance of moving parts. These reasons all produce vibration and noise, which must be paid attention to and avoided as far as possible in the process of installation. For the damaged parts that can not be repaired, they must be replaced to ensure that the system obtains a stable noise level.
2. Vibration reduction and interruption measures
When the gearbox reducer is installed, it should avoid resonance and noise between the fuselage and the base support and connectors as far as possible. One or more gears in the brushless DC gear motor often produce resonance in some speed range. Some gearbox requiring low transmission noise and vibration should choose high toughness and high damping basic materials to reduce the occurrence of noise and vibration.
3. Looseness of Brushless DC gear Motor Parts
During installation, the loosening of individual parts of BLDC motor (such as bearing pre-tightening mechanism, shafting positioning mechanism, etc.) results in inaccurate positioning of the system, abnormal position engagement, shafting movement, vibration and noise. This series needs to proceed from the design structure, try to ensure the stability of the connection of the various mechanisms, and adopt a variety of connection modes.
Among them, the adjustment of geometric accuracy of parts and components does not meet the requirements of the standard when installed, which results in resonance of parts and components of brushless DC deceleration motor, resulting in noise. Therefore, more efforts should be made to improve the installation process and increase the tooling.
1. Damage of transmission parts
During installation, the transmission parts are damaged due to improper operation, resulting in inaccurate or unstable motion of the system. The damage of high-speed moving parts results in oil film vibration or dynamic unbalance of moving parts. These reasons all produce vibration and noise, which must be paid attention to and avoided as far as possible in the process of installation. For the damaged parts that can not be repaired, they must be replaced to ensure that the system obtains a stable noise level.
2. Vibration reduction and interruption measures
When the gearbox reducer is installed, it should avoid resonance and noise between the fuselage and the base support and connectors as far as possible. One or more gears in the brushless DC gear motor often produce resonance in some speed range. Some gearbox requiring low transmission noise and vibration should choose high toughness and high damping basic materials to reduce the occurrence of noise and vibration.
3. Looseness of Brushless DC gear Motor Parts
During installation, the loosening of individual parts of BLDC motor (such as bearing pre-tightening mechanism, shafting positioning mechanism, etc.) results in inaccurate positioning of the system, abnormal position engagement, shafting movement, vibration and noise. This series needs to proceed from the design structure, try to ensure the stability of the connection of the various mechanisms, and adopt a variety of connection modes.
Among them, the adjustment of geometric accuracy of parts and components does not meet the requirements of the standard when installed, which results in resonance of parts and components of brushless DC deceleration motor, resulting in noise. Therefore, more efforts should be made to improve the installation process and increase the tooling.
Post a Comment:
You may also like: