Category
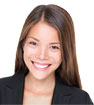
BLDC Motor Supplier

Home » BLDC Motor Application » Oscilloscope in BLDC Motor Industry
Oscilloscope in BLDC Motor Industry
Block diagram of the BLDC motor driver
The driver is made up of the power electronic device and the integrated circuit. It functions to control the launch, stop and braking of the electric motor by receiving the launch, stop and braking signals of the electric motor. Meanwhile, it can receive the position sensors' signals and signals of forward or backward rotation to control the on or off of the power tubes of the inverter-bridge, thus generating continuous torque. Last but not least, by receiving the speed instructions and the speed feedback signals, it can control and adjust the rotating speed, and provide protection and display.
From the above block diagram, it can be observed that MCU outputs six-channel PWM control signals via configuration of the register. The highest voltage is just 5V, which cannot directly drive the electric motor but control the electric motor's operation via the on and off the power tube. The driving circuit is usually made up of the driving bridge made up of several MOSFETs and the motor-driven bridge power tubes. Commutation of the high speed BLDC motor is equal to phase shift, which relies on detection of rotor's position. The inductive driving mode makes use of the Hall sensor to detect the rotor's position, while the non-inductive driving mode infers the rotor's position through detection and calculation of parameter changes, including current and voltage changes of the BLDC motor, during the rotation process, after which phase shift is realized.
Driver circuit working principle
Q1 to Q6 in the block diagram are the power field-effect tubes. When A and B phase are connected, we just need to open Tube Q1 and Q4, and stop the other tubes. At the moment, the current flows in the following route: the anode→Q1→Coil A→Winding B→Q4→Cathode. MCU sends PWM signals to Q1 grid but normally-open signals to Q4 grid. In this way, we can control the effective voltage of the drive motor by controlling the PWM signals' duty ratio from the input terminal of Q1. The other five steps of on after commutation are similar to the above step. The actually-measured waveforms of different phases are as below:
After the above PWM signal analysis of the BLDC motor controller, what new test experiences can ATO oscilloscopes offer?
512Mpts big data storage
In this case, when the engineer discovers any abnormality in the PWM signals of the BLDC motor driving voltage, it is to get triggered via the normal trigger method. Under the condition, the signals within the envelop should be analyzed in the zooming pattern and at a large time base. (Observe waveform details from the scaling window.) The PWM signals should reach more than dozens of K, and should ensure a high sampling rate. At the same time, PWM signals are accompanied by the current, encoder, and wave-carrier signals. The multi-channel observation, including observation of waveform time, sampling rate, and multiple channels, requires a large storage. Fig. 1 shows the BLDC motor PWM driving signals. When the storage depth is set to be 350M, the 7S waveform can be captured, and the sampling rate can reach as high as 50M Sa/s so that the waveform will not be distorted.
Double Zoom model + Intelligent labelling
As shown in Fig. 1, after capturing the waveform for a long time, how should the PWM driving signals or abnormal signals be analyzed? Besides, in terms of industrial server applications, when it is necessary to switch to different loads under different working conditions, and the driver waveform changes at different time or abnormal signals are found, to switch the whole load to a steady state takes a longer time. Besides, the waveform details should be observed at a large depth. Concerning the above situation, the ZDS4000 series oscilloscope can support the double Zoom mode under the prerequisite of ensuring a large storage depth. Meanwhile, the coefficient can be set for the two zooming windows, respectively. Coupled with the intelligent labeling, any signals one is interested in can be labelled. In Fig. , the waveforms within the main time base will be respectively enlarged in two Zoom windows. Zoom 1 is the PWM periodical signal, Zoom 2 is the oscillating waveform of certain peak of PWM. Under the prerequisite of a large storage depth, the sampling rate is 50M Sa/s. This can ensure authenticity of the waveform details. Additionally, the intelligent labeling function can be made use of to label on the main time base for example, and then the labeling points can be quickly found from Zoom 1 and Zoom 2. The labeling point of Zoom 1—the third peak of PWM can be observed. The oscillation situation and amplitude of the peak can be observed in Zoom 2.
ATO oscilloscope, relying on its 512M deep storage, double Zoom mode, template trigger, FIR hardware filter and intelligent labelling, can quickly and accurately position and analyze abnormal waveforms of the BLDC motor driver, thus providing a perfect solution plan for the waveform debugging of the BLDC motor industry.

The driver is made up of the power electronic device and the integrated circuit. It functions to control the launch, stop and braking of the electric motor by receiving the launch, stop and braking signals of the electric motor. Meanwhile, it can receive the position sensors' signals and signals of forward or backward rotation to control the on or off of the power tubes of the inverter-bridge, thus generating continuous torque. Last but not least, by receiving the speed instructions and the speed feedback signals, it can control and adjust the rotating speed, and provide protection and display.
From the above block diagram, it can be observed that MCU outputs six-channel PWM control signals via configuration of the register. The highest voltage is just 5V, which cannot directly drive the electric motor but control the electric motor's operation via the on and off the power tube. The driving circuit is usually made up of the driving bridge made up of several MOSFETs and the motor-driven bridge power tubes. Commutation of the high speed BLDC motor is equal to phase shift, which relies on detection of rotor's position. The inductive driving mode makes use of the Hall sensor to detect the rotor's position, while the non-inductive driving mode infers the rotor's position through detection and calculation of parameter changes, including current and voltage changes of the BLDC motor, during the rotation process, after which phase shift is realized.
Driver circuit working principle

Q1 to Q6 in the block diagram are the power field-effect tubes. When A and B phase are connected, we just need to open Tube Q1 and Q4, and stop the other tubes. At the moment, the current flows in the following route: the anode→Q1→Coil A→Winding B→Q4→Cathode. MCU sends PWM signals to Q1 grid but normally-open signals to Q4 grid. In this way, we can control the effective voltage of the drive motor by controlling the PWM signals' duty ratio from the input terminal of Q1. The other five steps of on after commutation are similar to the above step. The actually-measured waveforms of different phases are as below:

After the above PWM signal analysis of the BLDC motor controller, what new test experiences can ATO oscilloscopes offer?
512Mpts big data storage
In this case, when the engineer discovers any abnormality in the PWM signals of the BLDC motor driving voltage, it is to get triggered via the normal trigger method. Under the condition, the signals within the envelop should be analyzed in the zooming pattern and at a large time base. (Observe waveform details from the scaling window.) The PWM signals should reach more than dozens of K, and should ensure a high sampling rate. At the same time, PWM signals are accompanied by the current, encoder, and wave-carrier signals. The multi-channel observation, including observation of waveform time, sampling rate, and multiple channels, requires a large storage. Fig. 1 shows the BLDC motor PWM driving signals. When the storage depth is set to be 350M, the 7S waveform can be captured, and the sampling rate can reach as high as 50M Sa/s so that the waveform will not be distorted.
Double Zoom model + Intelligent labelling
As shown in Fig. 1, after capturing the waveform for a long time, how should the PWM driving signals or abnormal signals be analyzed? Besides, in terms of industrial server applications, when it is necessary to switch to different loads under different working conditions, and the driver waveform changes at different time or abnormal signals are found, to switch the whole load to a steady state takes a longer time. Besides, the waveform details should be observed at a large depth. Concerning the above situation, the ZDS4000 series oscilloscope can support the double Zoom mode under the prerequisite of ensuring a large storage depth. Meanwhile, the coefficient can be set for the two zooming windows, respectively. Coupled with the intelligent labeling, any signals one is interested in can be labelled. In Fig. , the waveforms within the main time base will be respectively enlarged in two Zoom windows. Zoom 1 is the PWM periodical signal, Zoom 2 is the oscillating waveform of certain peak of PWM. Under the prerequisite of a large storage depth, the sampling rate is 50M Sa/s. This can ensure authenticity of the waveform details. Additionally, the intelligent labeling function can be made use of to label on the main time base for example, and then the labeling points can be quickly found from Zoom 1 and Zoom 2. The labeling point of Zoom 1—the third peak of PWM can be observed. The oscillation situation and amplitude of the peak can be observed in Zoom 2.
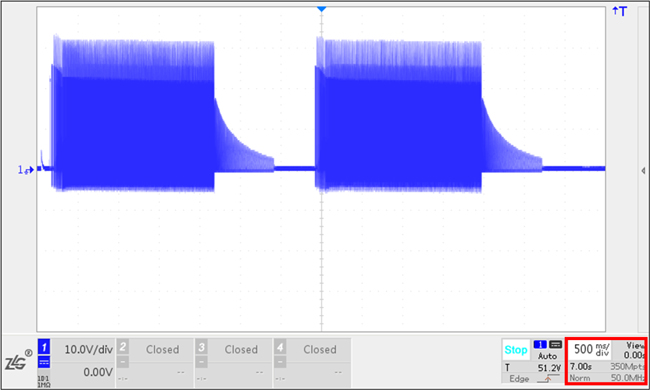
ATO oscilloscope, relying on its 512M deep storage, double Zoom mode, template trigger, FIR hardware filter and intelligent labelling, can quickly and accurately position and analyze abnormal waveforms of the BLDC motor driver, thus providing a perfect solution plan for the waveform debugging of the BLDC motor industry.
Post a Comment:
You may also like: