Category
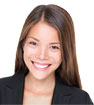
BLDC Motor Supplier

Home » BLDC Motor Controller » Technology Development of BLDC Motor Controller
Technology Development of BLDC Motor Controller
Brushless DC motor controller is mainly for controlling the speed, which process is to detect the speed of the brushless DC motor, compare its set values, and then control the power transistor through the control link in the control system. The control system includes many protection circuits, such as over-voltage and over-current protection.
Transition of Driver Controller
The driving controller of BLDC motor was mainly analog controller in the early stage, but in recent years it has gradually developed into digital controller. The control system of analog motor control system is relatively simple, easy to use and inexpensive. Due to technical and economic constraints, the analog motor control system has existed for a long time, but the analog control system itself has many shortcomings. The interference ability is poor, it can hardly be reused, and the control is not good. With the vigorous development of software technology, replacing hardware structure with software program effectively reduces the complexity of hardware circuit, reduces the volume specification of controller, makes modern control theory widely used, thus effectively improves the performance of control system. Therefore, digitalization of motor controller is the development direction of motor control in the future.
Transition of Processor
Up to now, there are generally three kinds of controllers for brushless DC motor: microprocessor, dedicated integrated circuit and modern digital signal processor. Because the motor control circuit composed of special integrated circuit is mainly applied to the control performance requirements are not high, the control method of the circuit is relatively simple, practical; However, due to the rapid development of modern technology in recent years, especially the wide use of BLDC motor in the household appliance industry, people have higher requirements for motor control performance, and the control accuracy and speed of micro-processing for motor can not meet people's needs.
Nowadays, modern DSP is widely used to solve the higher requirements for motor control performance. DSP integrates many functional modules and interfaces.
(1) FIFO buffer and baud rate generator
(2) Integrated Sampling and Holding Circuit and A/D Conversion Circuit
(3) Standard asynchronous and high-speed and synchronous serial ports are provided
(4) Provide multi-channel PWM output interface and input interface of sensor acquisition signal
It is precisely because these integrated modules reduce the requirements of the ATO BLDC motor controller for peripheral circuits, and have better software development tools, the price is relatively low, close to the price of the single chip microcomputer, but the cost performance is higher.
The operation speed of the digital signal processor of the ATO BLDC motor controller is relatively fast, which can be used in the motor control system of some complex real-time control algorithms, such as: kalman filter, the state estimate and parameter adaptive control and so on. These complex control method is very good to improve the performance of the motor control system. In addition, the application software program of digital signal processing can be programmed by electroplating assembly language or C language, or both of which can be used to write nested control program, thus providing great convenience for R&D personnel and glucoside in the research and development, debugging and application of motor controller.
Transition of Driver Controller
The driving controller of BLDC motor was mainly analog controller in the early stage, but in recent years it has gradually developed into digital controller. The control system of analog motor control system is relatively simple, easy to use and inexpensive. Due to technical and economic constraints, the analog motor control system has existed for a long time, but the analog control system itself has many shortcomings. The interference ability is poor, it can hardly be reused, and the control is not good. With the vigorous development of software technology, replacing hardware structure with software program effectively reduces the complexity of hardware circuit, reduces the volume specification of controller, makes modern control theory widely used, thus effectively improves the performance of control system. Therefore, digitalization of motor controller is the development direction of motor control in the future.
Transition of Processor
Up to now, there are generally three kinds of controllers for brushless DC motor: microprocessor, dedicated integrated circuit and modern digital signal processor. Because the motor control circuit composed of special integrated circuit is mainly applied to the control performance requirements are not high, the control method of the circuit is relatively simple, practical; However, due to the rapid development of modern technology in recent years, especially the wide use of BLDC motor in the household appliance industry, people have higher requirements for motor control performance, and the control accuracy and speed of micro-processing for motor can not meet people's needs.
Nowadays, modern DSP is widely used to solve the higher requirements for motor control performance. DSP integrates many functional modules and interfaces.
(1) FIFO buffer and baud rate generator
(2) Integrated Sampling and Holding Circuit and A/D Conversion Circuit
(3) Standard asynchronous and high-speed and synchronous serial ports are provided
(4) Provide multi-channel PWM output interface and input interface of sensor acquisition signal
It is precisely because these integrated modules reduce the requirements of the ATO BLDC motor controller for peripheral circuits, and have better software development tools, the price is relatively low, close to the price of the single chip microcomputer, but the cost performance is higher.
The operation speed of the digital signal processor of the ATO BLDC motor controller is relatively fast, which can be used in the motor control system of some complex real-time control algorithms, such as: kalman filter, the state estimate and parameter adaptive control and so on. These complex control method is very good to improve the performance of the motor control system. In addition, the application software program of digital signal processing can be programmed by electroplating assembly language or C language, or both of which can be used to write nested control program, thus providing great convenience for R&D personnel and glucoside in the research and development, debugging and application of motor controller.
Post a Comment:
You may also like: